The Curse of Apparent Cause Analysis (Updated)
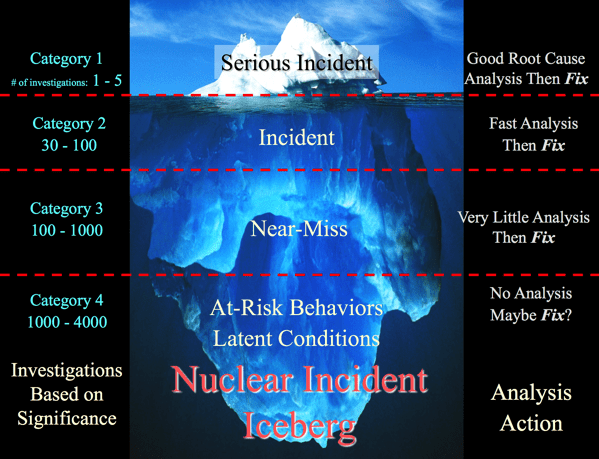
Why Write About Apparent Cause Analysis?
In March of 2006, I wrote about a problem (The Curse of Apparent Cause Analysis). What was the problem with Apparent Cause Analysis? People in the nuclear industry were taking a shortcut and thought that the results were “good enough.” I thought it was causing problems for the industry, and the problems needed fixing.
But before we go on, what is “Apparent Cause Analysis?”
What is Apparent Cause Analysis?
Here is a simple comparison chart from Lawrence Berkley Lab that should explain it…

Now, let’s look at the original article that I wrote back in 2006…
Original Article: The Curse of Apparent Cause Analysis

The original article in Root Cause Network™ Newsletter (Copyright © 2006, used by permission) created quite a stir.
- Some called me to praise the idea of more attention to serious incidents and improved proactive improvement.
- Others questioned my views about NOT analyzing seemingly simple near-misses with Apparent Cause Analysis.
- Some were really mad. They HATED the idea that what they had done for years was a curse to the industry.
16 Years Later – What Has Changed?
Here is the bad news: some are still using Apparent Cause Analysis in its original, substandard form. Some even recommend it to others!
The good news: Ten years later (March of 2016), many took my advice after the Nuclear Energy Institute (NEI) recommended reducing the cumulative impact of corrective action programs (Efficiency Bulletin 16-10, Reduce Cumulative Impact From the Corrective Action Program).
Even better news: Some adopted our essential root cause analysis process and tools (published in 2015) to reduce their efforts while still getting good results when investigating simple incidents (instead of using Apparent Cause Analysis).
Unfortunately, I still hear about facilities outside the nuclear industry being misled into the fiction that they can just do 20% of the effort and get 80% of the results by applying Apparent Cause Analysis to improve safety, quality, patient safety, or industrial productivity. I guess they never heard about the problems Apparent Cause Analysis caused in the nuclear industry. HERE is an example.
I know they will eventually learn the difficult lesson that Apparent Cause Analysis doesn’t work (after wasting time and effort and not getting the promised improvements). But I worry about the lives lost, the injuries that will not be prevented, the quality incidents that will happen, and the productivity lost while implementing a failed technique – Apparent Cause Analysis.
Apparent Cause Analysis – My Advice
So, my advice has changed just a little in 16 years…
1. Expand good root cause analysis to all precursor incidents. See the article “What is a Precursor Incident?” for the definition of a Precursor Incident. See the article “Deciding When to Investigate a Precursor Incident (What’s in the Diamond?)” to start defining when to investigate a minor incident.

2. Learn to use the Essential TapRooT® Process (shown above) and Techniques to investigate low-to-medium risk incidents. Click HERE for information about the 2-Day TapRooT® Course to learn these techniques.
3. STOP investigating minor incidents that don’t deserve to be investigated. Instead, categorize and trend them using advanced trending techniques. Learn more about advanced trending techniques HERE. Or attend our pre-Summit Course on trending. Get more information HERE.
4. Save the effort you might have spent doing 1000 short-cut analyses and then fixing the assumed problems. Instead, put that effort into a targeted PROACTIVE improvement program based on good root cause analysis and proactive tools to help you stop human error. Read about our course teaching how to proactively improve HERE.
5. When you get really interested in improving performance, learn more about TapRooT® RCA and improving human performance by attending the 5-Day TapRooT® Advanced Root Cause Analysis Team Leader Course and the Stopping Human Error Course.

6. Attend the Global TapRooT® Summit to learn the latest performance improvement and root cause analysis best practices. Find out more about the Summit by CLICKING HERE.
But whatever you do:
Please stop fooling yourself about
getting something for nothing!