Practical, Efficient, Effective Human Performance Tools for the Nuclear Industry
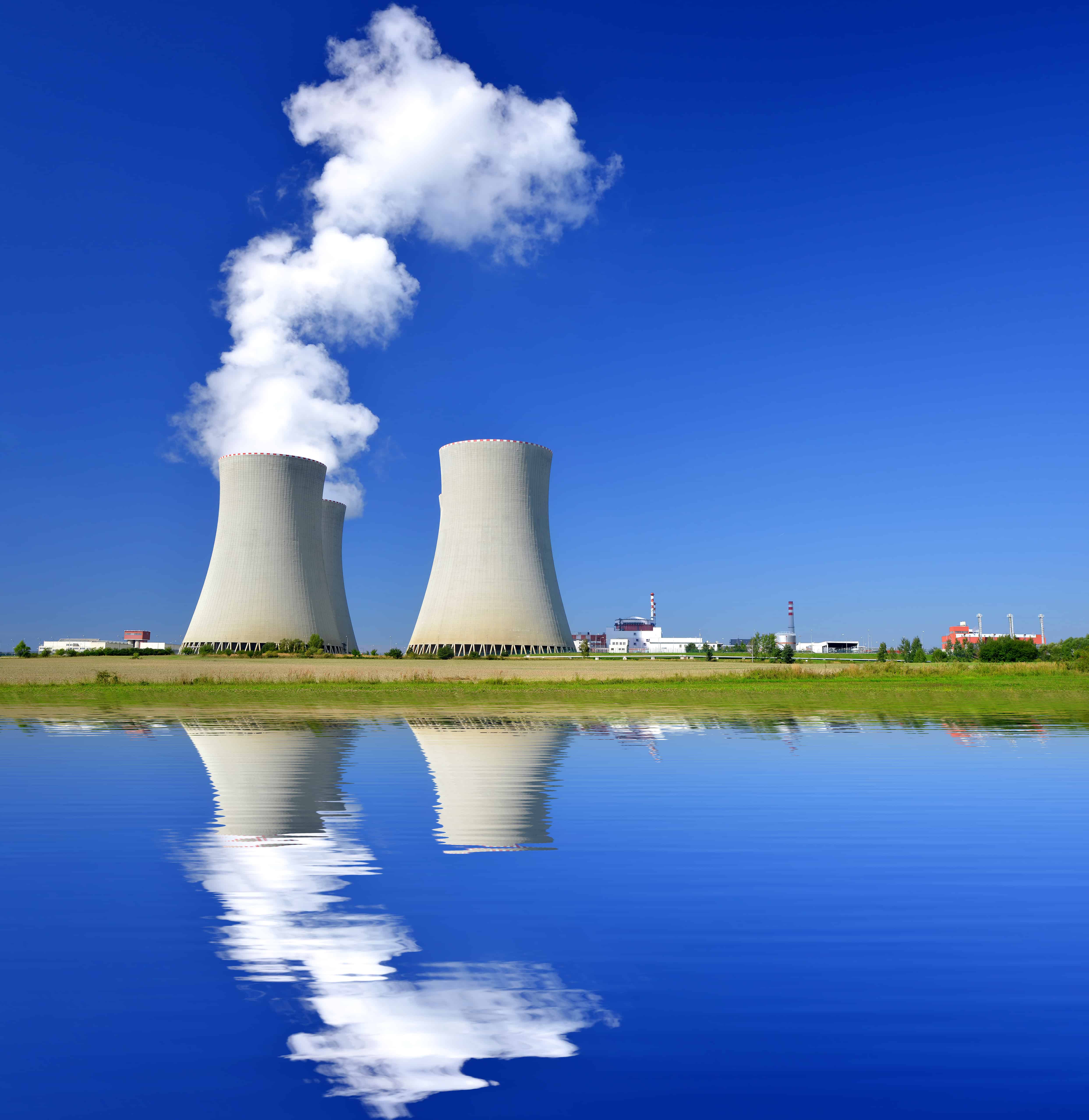
Problems with Human Performance in the Nuke Industry
Human Performance (Hu) History
Back in the 1980s, INPO decided that nuclear plants needed better human performance. They started the development of their first human performance (Hu) tool – HPES (or the Human Performance Evaluation System). I was just leaving the Nuclear Navy with an MS in Nuclear Engineering with an emphasis on Human Factors and interviewed with INPO to help develop HPES. I didn’t take the job, but I ended up working with the guys at INPO (Joe Bishop and others) by reviewing and suggesting improvements to HPES, including the Management System portion of the tool.
The years passed, and additional tools were developed. More and more until the list of tools included:
- Procedure Use
- Procedure Adherence
- Place Keeping
- Independent Verification
- Three-Way Communications
- Pre-Job Brief
- Post-Job Brief
- Personal Safety Assessment
- Observation and Coaching
- Concurrent Verification
- Questioning Attitude
- STAR
- Time Out (Stop When Unsure)
- Attention to Detail
- Management of Change
- Error Traps and Precursors
- Validate Assumptions
- Do Not Disturb Sign
- Conservative Decision-Making
This isn’t a standard list. There really isn’t a standard. The techniques were modified by the Department of Energy for their weapons and research plants. Various consultants added and subtracted from this list as they brought the techniques to other industries. Also, the techniques may vary depending on the teacher you learned them from and the version you learned (yes, since the start of the development of these techniques in the 1990s, they have been “improved” and revised). Therefore, the techniques may vary in their names and complexity.
In the last decade, the Nuclear Industry has been challenged to cut costs by reducing the complexity of the performance improvement tools that they use. And one thing that had grown quite complex was the Hu programs at nuclear plants.
In addition to the complexity of the large number of tools listed above, some managers in the nuclear industry started to realize that at least some of the Hu tools might not be as effective as they were advertised to be. Some tools seemed to result in blame. They got a bad name because, after an incident, investigators could always spot the lack of the use of a tool that would have prevented the incident.
Nonetheless, once a tool like Hu is adopted across an industry, it develops true believers. I’ve found it difficult to get a true believer to look at the tool critically, even if one of their tools is to “Challenge Assumptions” and another is “Questioning Attitude.”
The Time Has Come to Revisit Hu Programs
Therefore, we believe that the time has come to critically assess Hu and address the problems with Hu Programs in the Nuclear Industry. This critical look may provide a more effective group of Human Performance Improvement Tools that are based on human factors research and best practices. These could then be applied selectively based on the most pressing problems at a particular plant.
So, what did we do? We researched the Hu Programs and studied the tools’ human factors basis. We discovered which tools worked and why and which tools were not tools but rather a management philosophy. We also found additional ideas from human factors that should be included in Human Performance Improvement Programs. Finally, we identified Hu Tools that should be avoided (or perhaps discarded).
To document our work, we wrote a book:
Get more information about the book HERE.
After writing the book, we decided to develop a course to help people understand the theories behind human performance improvement and how to create a custom, efficient, effective human performance improvement plan. Now that course is available to help you improve your Hu Program.
What Should Nuclear Plant Hu Managers Do?
Challenge the Hu Program status quo! Attend the course – Stopping Human Error – and get ideas to improve your human performance improvement efforts.
When can you take this course? Either on October 25-26 or April 24-25.
Where are these courses being held? The October course is being held at the Embassy Suites in Austin, TX. The April course (Pre-Summit) is being held at the Margaritaville Lake Resort, Lake Conroe, near Houston, TX.
This Course Isn’t for Everyone. You Must Have a Questioning Attitude and Be Ready To Challenge Assumptions!
Of course, you must come to the course with a questioning attitude. You should be ready to challenge your assumptions. Why do I say this? Because I was talking to a safety/human performance manager at a nuclear plant, and he got mad. He said his Hu Program worked great. It didn’t need to be tampered with. I tried to explain just one of the potential faults with just one tool – Error Traps and Precursors. You can see more about my critique of that tool here…
What Are the Human Error Traps & Precursors? [Can You Spot Them?]
He told me that he did his job just fine without my help. He maintained that his company’s safety performance proved that the tools worked great. I asked:
“How do you know that?”
After all, there might be more efficient and effective methods. Maybe his statistics could be better or achieved with less effort. He was insulted that I challenged his assumptions. I thought I was pointing out the faults of the Human Error Traps and Precursors tool … not his application of the tool. That’s what I get for having a questioning attitude.
So, if you can’t look at your program with a critical eye (with a vision to improve things), then you probably SHOULD NOT attend this course.
If, on the other hand, you are ready to make your Hu Program more efficient and effective, this course comes with a guarantee:
Attend this course, go back to work, and use the techniques you have learned to stop human error. If you don’t find new ways to improve human performance and if you and your management don’t agree that your efforts to improve human performance are much more effective, just return your course materials and we will refund the entire course fee.
What’s in the Stopping Human Error Course?
Here are some of the concepts we will help you understand:
- The causes of human error
- Human factors design best practices
- Methods to find error-likely
Here is the course outline:
-
Day 1 (8:00am to 5:00pm)
- Foundations of Improving Human Performance
- Human Performance – What Should You Expect?
- Three Human Reliability Best Practices
- Mistake Proofing
- Resilience
- Safeguards
- Using TapRooT® Root Cause Analysis for Reactive Problem Analysis
- Human Performance Improvement Technology (Catch Your Own Mistakes)
- STAR
- Questioning Attitude
- Attention to Detail
- Time Out
- Error Traps & Precursors
- Validate Assumptions
- Work Direction/Finding Error-Likely Situations
- Pre-Job Hazard Analysis
- Pre-Job Brief
- Personal Safety Assessment
- Post-Job Brief
- Training
- Systematic Approach to Training
- Using Procedures to Improve Human Performance
- Procedures Best Practices
- Procedure Use and Adherence
- Place Keeping
Day 2 (8:00am to 5:00pm)
- Communications
- 3-Way Communication
- Do Not Disturb Sign
- Management System
- Conservative Decision Making
- Stopping Normalization of Deviation
- MOC
- Quality Control
- Independent Verification
- Concurrent Verification
- Human Factors Engineering
- Best Practices (Spot Bad Practices)
- Proactive Use of CHAP
- Hazard/Target Elimination or Substitution
- Improvement Exercise
- What Should You Improve/Which Tools Will Work Best for You?
- Sample Plan
- Present Your Plan (Benchmarking/Feedback)
- Techniques to help supervisors and workers prevent human errors
- CHAP (Critical Human Action Profile)
- Human Performance improvement Technology
- Designing your human performance improvement program.
With the exercises built-in to try some of the techniques, this will be an active, quick-moving 2-day course that presents the advantages and disadvantages of each technique.
You will leave this course with a clear understanding of methods to improve human performance and a custom plan to apply the best of those methods at your company to achieve great gains in safety, quality, or operational and maintenance performance (all of which depend on human performance).
Participants will also receive the new book, Stopping Human Error, a $99.95 value, as part of the course materials. In addition, participants will receive a certificate of completion and a 90-day subscription to TapRooT® VI Software, our dynamic cloud-based root cause analysis software.
REGISTRATION
To register for the new Stopping Human Error Course, click on your choice of the dates below…
The Stopping Human Error Course on October 25-26.
The Stopping Human Error Course on April 24-25.
Don’t miss out! The October course is rapidly approaching, and you need to implement these improvements as soon as possible!